Home » Articles posted by Oskar Graham
Author Archives: Oskar Graham
The Importance of Roofing Maintenance
North Port FL Roofing maintenance is essential to protecting your facility and ensuring that your roof warranty remains valid. Performing routine inspections and taking action on minor problems can prevent severe and expensive damage in the future.
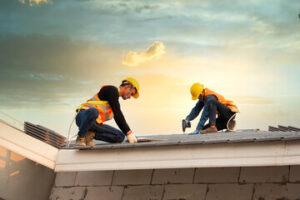
A professional inspector looks at the condition of the shingle from the ground to see signs of curling, peeling, and missing shingles. They also look at the condition of field drains and auxiliary drains.
Asphalt shingles are a budget-friendly and durable roofing option for residential homes. They offer a wide selection of color options, styles, and shingle grades to accommodate many different home exteriors. The affordable material also offers superior resistance to weather elements such as wind, rain, and ice. In addition, most shingle types can be found with varying levels of fire and hail resistance.
However, despite the durability of asphalt shingles they are not impervious to damage or premature wear. Common roofing maintenance tasks include repairing damaged or missing shingles, replacing cracked or torn flashing, caulking or patching around chimneys, skylights and other roof penetrations, and maintaining the integrity of the gutter system. These routine tasks will help prevent leaks and protect the interior of the home from water damage.
A common issue with asphalt shingles is the growth of moss and algae. It is important to regularly remove this growth using a gentle cleaning solution, preferably one with a bleach and water blend. Do not use a power washer, as this can dislodge the protective granules on the shingles.
Another issue commonly seen on asphalt shingles is the loss of the heavy oils in the paper. This can be caused by the sun’s rays or from exposure to chemicals in the roof environment. This process happens most rapidly along eaves and complex rooflines where the water is channeled more quickly. Eventually this can cause the shingle to shrink, which exposes the nail heads and causes water to seep into the house.
The best way to extend the lifespan of your asphalt shingle roof is through regular maintenance and inspections. Be sure to follow the recommended maintenance instructions provided by the manufacturer of your shingles. This will help ensure that the warranty on your shingles is in good standing and that the roof is functioning properly to protect your home. Additionally, a well-maintained roof will increase the comfort of your family and add value to your home. It is easy to ignore your roof until there is a problem, but regular maintenance will keep your home in good condition and protect your investment.
Wood
Wood shingles and shakes are an attractive roofing option for homeowners who want to maintain a rustic, natural look. However, these roof fittings must be regularly maintained to extend their useful life. The materials are vulnerable to weathering, which degrades wood by soaking in water and sunlight, and to organisms that attack the material. These problems can be mitigated with regular cleaning and treatment.
Wood preservatives are available that arrest the degradation caused by moisture and light. These are usually surface treatments that contain a mixture of waxes, resins and fungicides to resist moisture uptake and UV radiation. They can also contain pigments that absorb ultraviolet radiation to keep the wood from fading or changing color. Some treatments contain algaecides to kill mosses and mildews, which degrade the roof surface.
The longevity of a wood roof is also related to the amount and temperature of rainfall it receives. Rainfall that is hot and wet will cause wood to degrade more quickly than rain that is cool and dry. In addition, the pitch of the roof influences how quickly a roof will shed water; steeper roofs will tend to shed more rapidly than shallow ones. Overhanging trees and vegetation also retard the shedding of water by shading the roof and dropping debris that can retain moisture.
In the Pacific Northwest, cedar is the preferred wood for shingle and shake roofs because it holds up well in wet conditions. Other species that can be used include western redcedar, bald cypress and southern hemlock. However, all woods eventually degrade. Chemicals in the soil and rain slowly degrade the wood, and repeated wetting and drying cause physical changes to the shake or shingle.
The type of shingle or shake also affects how long it lasts. Shingles are machine-sawn, with cuts that range from along the grain to against it. Shakes are hand-split, so one of the shakes’ sides is always along the grain; this gives the shakes more strength and durability. The quality of the shingle or shake is important, too. A grade of #1 is the best, taken from the heartwood and containing only edgegrain with no defects; this is typically used for roofing or sidewalls. A grade of #2 is more economical, but allows a certain amount of flatgrain and knots above the clear portion; it is used for siding and as a starter course.
Metal
Metal shingles are designed to be long-lasting and durable, but they still require maintenance to ensure their durability. Surface maintenance involves a general look-over and includes things like removing dirt, debris and scuff marks, as well as checking for signs of corrosion or damage.
For most metal roofs, a soft-bristled brush or a non-metal scrubber and a solution of water and detergent should do the trick. A mild solution of trisodium phosphate (“TSP” found in hardware stores), laundry detergent, or even non-abrasive all-purpose cleaner will work, but make sure that your cleaning solution is not too strong, as it may damage the protective coating on the roof.
Walking on a metal roof is usually not recommended, as it can cause scratches and damage the panels. It’s also important to avoid walking in low points and over support purlins, as this can damage the panel seam and lead to leaks. Keeping nearby trees properly trimmed can also prevent branches from rubbing against the roof, which can scratch or scuff the paint and cause further damage.
If you have a screw down metal roof, it’s a good idea to check the screws every 20-30 years. They can loosen over time due to lack of expansion and contraction, which in turn can lead to rust spots. The screw head should be inspected for deterioration as well, as holes in the heads can allow water to get inside and potentially damage the underlayment.
It’s a good idea to clean your gutters and drains at least twice a year, preferably in the spring and fall. Cleaning your gutters will help them function more efficiently, and will ensure that they are not clogged with leaves or other debris. Pooling or standing water can cause corrosion, as well as leaks in the home. A professional can recommend and install a drainage system that will help prevent these issues. It’s also a good idea to inspect for any dents or punctures from storms, hailstorms or falling debris. These should be repaired as quickly as possible to minimize damage and extend the life of the metal roof.
Composite Shakes
Cedar shakes are beautiful roofing material that is durable, weatherproof and has a long lifespan. Like any other roofing material, it needs regular maintenance and inspections to prevent damage. If left unchecked, the natural materials that make up cedar shakes can deteriorate and lead to problems such as mildew growth, mold, moss, rot, small cracks, wood damaging fungi and moisture in the attic. To avoid these issues, homeowners need to perform visual inspections of their shake roofs at least once a year and clean the shakes periodically with a soft brush or low-pressure washer to remove dirt and debris. Moreover, it is recommended to apply a cedar-friendly sealant or wood preservative every few years to protect the shakes from moisture and UV damage.
Composite shingle manufacturers have developed products that are designed to mimic the look of slate and shake shingles while also providing excellent durability. DaVinci Roofscapes, for example, offers several faux shake and slate products including Bellaforte shake that is molded from actual cedar shakes and multi-width slate products that give the appearance of hand-split real slate.
These products are crafted using a 3D computerized image of the original product and exact molds for liquid polymer casting that are carefully set in place to replicate natural details. The finished product is virtually indistinguishable from the real thing, down to the chisel marks for a more authentic look.
Because they are made from a polymer, these products have a long life span and do not require the periodic re-staining and oiling that traditional shakes require. In addition, they are fire resistant and do not rot, dry out or decay, making them an attractive alternative to the more vulnerable natural materials that were used in the past.
While these materials may be a good choice for new construction, it is important to note that they are not as effective in protecting buildings during severe weather such as hail storms. In addition, they tend to be more expensive than other roofing products that can offer a Class 4 Hail Impact Rating.
When it comes to the protection of older historic properties, however, the best option is CeDUR. It is an energy efficient roofing product that can be installed over existing shingle or shake roofs and improves the R-Value of the home. This insulation helps to keep the home warmer in the winter and cooler in the summer.
The Importance Of Safety Precautions During Roof Repairs Or Installations
Keeping safety precautions in mind while working on roofs is essential to ensure that the job gets done quickly and efficiently. This includes preparing the work area, clearing debris and obstacles, and securing materials and tools.
It’s also important to maintain three points of contact with the roof surface at all times. This means having both feet and one hand on the ladder. For your roofing needs, contact Roofing Companies Temple TX today!

Ladder Safety
Ladders are a critical tool for any professional tradesperson who works on roofs, but they can be dangerous if not used properly. Hundreds of people are injured each year by ladder accidents, most of which are preventable with the proper maintenance and safety precautions.
When using ladders, always read and follow the instructions. Avoid overloading a ladder, and never use it in an area with electrical hazards such as power lines. Look up before handling a ladder, and always maintain three points of contact when climbing (two hands and one foot or two feet and one hand).
Ladders should be regularly inspected for defects. This includes checking the feet of the ladder, which are designed to grip the ground and prevent slipping, and the rungs for cracking, wear, and other problems that could lead to instability or falling off. The ladder should also be inspected for loose screws, bolts, or rivets that can cause problems and should be tightened. If the ladder has optional accessories like stabilizers, these should be inspected as well. They should be in good working condition, and any that are worn or damaged should be replaced as recommended by the manufacturer.
The most common cause of ladder accidents is human error, and this can be prevented by taking the necessary safety precautions when using a ladder. Whether it’s choosing the right ladder for the job, inspecting it before climbing, or knowing how to set it up safely, these simple steps can save lives and reduce injuries.
If you’re a homeowner or a professional tradesperson, it’s important to take the time to understand and practice ladder safety, as these precautions can protect you from injury and save you money by reducing the number of ladder-related repairs or replacements. By following these tips, you can ensure your ladder is safe to use and that it’s ready to help you complete your next roofing project. Remember, the most important part of a ladder isn’t its length or structure – it’s the distance that a worker falls during a fall that matters!
Fall Protection
Falling from a roof is not just a potentially deadly injury, but also an economic liability. If a worker falls, he or she must take time off work to recover, which means a loss of productivity and revenue. In addition, medical bills and legal fees are costly. For these reasons, a comprehensive safety program is crucial for any business that does roofing.
While many contractors understand the importance of following proper safety precautions, some may view implementing these measures as an obstacle to productivity and profitability. The act of climbing up and down to fasten harnesses or install guardrails can certainly slow down the rhythm of a job. However, that momentary delay is insignificant compared to the long-term effects of a free fall from a roof.
Facility and maintenance managers need to plan for these risks before beginning roof repairs or installations on commercial buildings. They should conduct a risk assessment and choose the right equipment. They should also ensure that technicians receive appropriate training and are fully aware of the responsibilities and obligations of the equipment they use.
A wide range of fall protection systems is available for roofers to protect them from falling hazards. Examples of these include mobile 360 guardrails, safety net systems, self-retracting lifelines, and a variety of other options. These devices provide a dependable anchor point to attach workers’ harnesses, stopping them from hitting a lower surface when they fall. If it is infeasible to use these systems or they present a hazard, then a detailed alternative fall protection plan should be developed and followed.
Additionally, workers must always be on the lookout for tripping and slipping hazards when working on a roof. Air hoses and power cords for nail guns, as well as discarded equipment, can create dangerous trip points. Organizing these items as they are removed and staging new materials in safe locations will eliminate this danger.
A well-planned rooftop safety program can help prevent falls that lead to costly injuries and legal situations. A single slip-up or rushed decision could have devastating results for a worker, his or her family, and the company. By planning for these risks and implementing the right equipment, facilities managers can improve front-line workers’ job performance while simultaneously reducing their liability risks.
Personal Protective Equipment (PPE)
Personal protective equipment (PPE) includes a variety of items worn by workers to minimize exposure to hazards. These include clothing, eye and ear protection, breathing equipment, and gloves. PPE must be correctly fitted and maintained to provide the protection it was designed for. It imposes a barrier between the worker and their working environment and can be physically taxing on the body. This can cause discomfort, which discourages wearers from using it and could result in injury or ill health.
When used correctly, PPE prevents the spread of infection. In hospital settings, for example, it can protect patients who have compromised immune systems from being exposed to infectious materials. It can also help prevent the spread of viral and bacterial contaminants from blood, body fluids, or respiratory secretions.
It is important to identify hazards and conduct a risk assessment before implementing a PPE program. A thorough risk assessment will look at work practices, job procedures, equipment, plant layout, and individual factors. It should also examine the different types of potential hazards. Some hazards may require more than one type of PPE. For example, working with chlorine requires skin and respiratory protection because it irritates the skin and mucous membranes. Reviewing safety data sheets and conducting a workplace trial help choose the appropriate PPE.
Once the appropriate PPE has been chosen, it should be inspected regularly to ensure it is fit for use. Inspecting PPE includes evaluating the fit, ensuring that it is clean and in good repair, and checking that it meets manufacturer specifications and that it is stored properly. Regular inspections should be conducted by the person responsible for purchasing, inspecting, and maintaining the PPE or a designated employee.
The PPE program must be an integral part of a comprehensive hazard control program. It should involve management, safety and medical personnel, supervisors, a health and safety committee, or individuals and suppliers of the PPE. Training should be provided regularly, and re-evaluation of the program should take place on an ongoing basis. PPE should never be seen as a substitute for eliminating or controlling the hazard itself.
Working on Roofs
Working on roofs can be extremely dangerous if you don’t take the proper precautions. Even the smallest mistake could lead to a serious accident, such as falling off of the roof because you were wearing your pants too loose and caught them on the ladder or you tripped over a nail that was sticking out of the roof surface.
In addition to providing fall protection, employers should provide a safe work plan, designate a safety monitor, and ensure that workers understand their tasks, responsibilities, and safety protocols. They should also encourage collaboration and teamwork to ensure that work is being done efficiently, correctly, and safely. Regular check-ins are an excellent way to keep track of any issues or potential hazards and identify the need for additional safety precautions.
Another important aspect of workplace safety on roofs is ensuring that the work area is clear and unobstructed. This includes removing any objects that may be in the way, such as furniture, equipment, or debris. It is essential to also block off the work zone from passersby so that they do not inadvertently encounter any hazards. It is also important to remove any tripping hazards, such as loose ladder legs or stray tools that could cause people to trip and fall. In addition, all workers should be aware of any electrical hazards and should use non-conductive equipment when working near electricity.
Ideally, all roofing accidents can be prevented through common sense and the implementation of workplace best practices. However, there are some situations where this is simply not possible and edge protection must be provided to isolate workers from the risk of falling off a roof. This can include short-duration works such as repairs and inspections that only last minutes, but should still be considered during the risk assessment process. Other forms of isolation can be achieved through the use of restraint systems, work positioning systems, safety nets, or safety mesh. Lastly, all workers should be trained in emergency preparedness and know what to do in the event of an incident or near-miss.